Struggling with inefficient flow control in your systems? Outdated valves often lead to leaks, energy waste, and costly downtime, disrupting operations and budgets. As leading smart valve manufacturers, we provide reliable, high-performance butterfly valve solutions designed for seamless integration and optimal efficiency, ensuring your systems run smoothly.
A butterfly valve is a type of quarter-turn valve primarily used to regulate the flow of fluids (liquid or gas) within a pipe. It features a circular disc mounted on a central stem. When the valve is closed, the disc blocks the passageway. A 90-degree rotation of the stem moves the disc parallel to the fluid flow, allowing passage. Their simple design makes butterfly valves compact, lightweight, and cost-effective for a wide variety of applications.
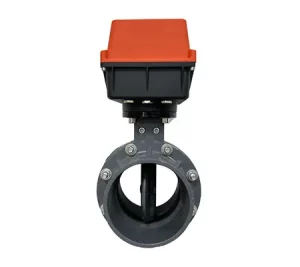
UPVC electric butterfly valve
What Exactly is a Butterfly Valve and How Does it Work?
A butterfly valve belongs to the family of quarter-turn valves, meaning a 90-degree turn of the handle or actuator moves it from fully open to fully closed, or vice versa. The core component is the valve disc, often simply called the disc, which is positioned in the center of the pipe. A stem passes through the disc and connects it to an external control mechanism – typically a handle, lever, or actuator.
When the butterfly valve is in the closed position, the disc is perpendicular to the fluid flow, effectively sealing the pipe. The effectiveness of this seal depends on the valve design and the seat material. To open the valve, the stem rotates the disc by 90 degrees, aligning it parallel with the flow direction. This allows fluid (liquids and gases) to pass through the valve body with relatively low obstruction. The position of the disc can also be adjusted to throttle or regulate the flow rate, although they are generally better suited for on/off shut-off applications compared to fine-tuned control valves.
The simplicity of the valve design – fewer moving parts compared to, say, a gate valve – translates to lower manufacturing costs, lighter weight, smaller installation footprint, and easier maintenance. This makes the butterfly valve a highly popular choice across numerous industries. As manufacturers, we focus on optimizing this simple design for maximum durability and performance.
Exploring the Different Types of Butterfly Valves
Butterfly valves come in several primary valve types, mainly distinguished by their body style and how they connect to the piping system. Understanding these differences is key to selecting the right valve for your specific needs.
- Wafer Type: This is the most common and generally most economical butterfly valve body style. It’s designed to fit between two pipe flanges. Long bolts extend from one flange through the valve body to the other flange, clamping the valve in place. Wafer style butterfly valves are typically easier to install and lighter, but they cannot be used as end-of-line valves (i.e., where only one flange is connected) as there’s no way to secure the valve body if the downstream piping is removed.
- Lug Type: Lug butterfly valves feature threaded inserts (lugs) around the valve body. These lugs allow the valve to be installed into a system using separate bolts for each flange. A key advantage is that one side of the piping can be disconnected while the lug style valve remains attached to the other side, allowing for end-of-line service. This feature is crucial for maintenance or system modifications where isolating sections is necessary. While slightly more expensive and heavier than wafer types, the lug design offers greater versatility.
- Flanged Type: Less common, these butterfly valves have flanges cast or attached directly to the valve body, similar to gate or ball valves. They are bolted directly to the mating pipe flanges. This design is often used in larger butterfly valves or high-pressure applications, providing a very secure connection.
Beyond body styles, butterfly valves are designed with different seating mechanisms, like the resilient seated butterfly valve (where the disc seals against a soft, often EPDM or Viton, seat) and high performance butterfly valves (often featuring metal seats for demanding conditions). We manufacture a broad range of sizes and types to meet diverse operational requirements.
Concentric vs. Eccentric: What’s the Difference in Butterfly Valve Design?
The relationship between the stem centerline, the disc centerline, and the seat determines whether a butterfly valve is concentric or eccentric. This valve design difference significantly impacts performance, suitability for different applications, and service life.
-
Concentric (Zero Offset): In a concentric butterfly valve, the stem passes through the centerline of the disc, and the disc itself is centered in the valve bore. The seat is typically a resilient (soft) material lining the inside of the valve body. When the disc closes, it makes contact with the full circumference of the seat simultaneously. This design is simple, cost-effective, and suitable for low-pressure applications and general shut-off duties in water systems, HVAC, and light industrial processes. The primary limitation is that the disc is constantly in contact with the seat during rotation, leading to wear over time, especially in abrasive or high-cycle applications.
-
Eccentric (Offset): Eccentric butterfly valves feature one or more offsets of the stem relative to the disc and seat centerlines.
- Single Offset: The stem is offset from the centerline of the disc. This was an early design to reduce seat wear.
- Double Offset (High Performance Butterfly): This is the most common eccentric design. It has two offsets: (1) the stem is offset from the centerline of the disc, and (2) the stem is offset from the centerline of the valve bore/seat. This geometry causes the disc to “cam” into the seat only during the last few degrees of closure, significantly reducing friction and wear during opening and closing. Double offset butterfly valves can handle higher pressures and temperatures than concentric designs and offer better sealing and longer life, making them suitable for more demanding industrial applications, including chemical processing and power generation.
- Triple Offset: Adding a third offset, which is the conical seat/disc sealing surface angle, creates a triple offset butterfly valve. This design achieves a bubble-tight, metal-to-metal seal without elastomers, making it ideal for high-pressure, high-temperature, cryogenic, and severe service applications, including gas and steam. The triple offset design eliminates friction during operation, providing exceptional durability.
As manufacturers, we produce both resilient seated and high performance double offset and triple offset butterfly valves to meet diverse operational requirements, ensuring optimal performance even under challenging temperature and pressure conditions.
How is Actuation Handled in Butterfly Valves?
Actuation refers to the mechanism used to open and close the butterfly valve. Because they are quarter-turn devices, butterfly valves are available with a variety of simple and powered actuation methods. The choice depends on valve size, torque requirements, operating environment, speed of operation needed, and the level of automation desired.
-
Manual Actuation:
- Lever Handle: Common for smaller butterfly valves, a simple lever provides quick on/off operation. It usually includes a locking mechanism or position indicator. Requires manual effort, which can be significant for larger valves or those under high pressure.
- Gear Operator: For larger butterfly valves or those requiring higher torque to operate, a handwheel connected to a gearbox (gear operator) is used. The gearbox multiplies the input force, making manual operation easier, albeit slower than a lever.
-
Powered Actuation:
- Electric Actuator: Uses an electric motor and gearing to rotate the valve stem. Electric actuators offer precise control, including throttling capabilities, and can be easily integrated into automated systems (like DCS or PLC). They are available in various voltages and enclosure types (weatherproof, explosion-proof). For applications requiring fine control, a Proportional rotary actuator can modulate the valve position accurately based on an input signal.
- Pneumatic Actuator: Uses compressed air acting on a piston or diaphragm to generate motion. Pneumatic actuators are known for their fast cycling speeds, reliability, and inherent safety in hazardous environments (no spark risk). They often require solenoid valves and air lines for control. They can be spring-return (fail-safe open or closed on loss of air pressure) or double-acting (air pressure required for both opening and closing).
- Hydraulic Actuator: Similar to pneumatic, but uses hydraulic fluid (usually oil) instead of air. Hydraulic actuators can generate very high torque, making them suitable for the largest butterfly valves or extremely high-pressure applications.
The selection of the actuator type is critical for reliable valve operation and system integration. Factors like available power sources, required speed, fail-safe requirements, and control system compatibility must be considered.
What Materials Are Commonly Used for Butterfly Valve Components?
The choice of materials for butterfly valve components (valve body, disc, stem, seat) is crucial for ensuring longevity, compatibility with the fluid medium, and resistance to corrosion and operating conditions. Butterfly valves feature components made from a variety of materials:
Component |
Common Materials |
Considerations |
Valve Body |
Cast Iron, Ductile Iron, Carbon Steel, Stainless Steel (e.g., 316 stainless steel), Alloys, PVC/CPVC |
Strength, pressure rating, corrosion resistance, cost, temperature limits |
Disc |
Stainless Steel (304, 316 stainless steel), Ductile Iron (often coated), Bronze, Alloys, PVC |
Corrosion resistance to fluid, strength, abrasion resistance, cost |
Stem |
Stainless Steel (various grades), Monel |
Strength (torque transmission), corrosion resistance |
Seat |
EPDM, Buna-N (Nitrile), Viton, PTFE (Teflon), Metal (in high-performance valves) |
Fluid compatibility, temperature range, sealing capability, abrasion resistance |
- EPDM (Ethylene Propylene Diene Monomer): Excellent for water systems, wastewater, glycols, and some mild chemicals. Good temperature range (-40°F to 250°F / -40°C to 121°C). Not suitable for oils or hydrocarbon solvents. Widely used in HVAC and municipal water applications.
- Buna-N (Nitrile): Good for petroleum oils, fuels, water, and hydraulic fluids. Moderate temperature range. Commonly used in oil and gas applications.
- Viton (FKM): Excellent resistance to a broad range of chemicals, oils, fuels, and high temperatures (up to 400°F / 200°C). More expensive than EPDM or Buna-N. Used in demanding chemical and high-temperature services.
- PTFE (Teflon): Extremely wide chemical compatibility and good temperature range. Often used as a seat material in high performance butterfly valves or as a resilient seat, sometimes encapsulated over an elastomer core.
- Metal Seats: Used in double offset and triple offset butterfly valves for high temperatures, high pressures, or abrasive services where elastomers would fail. Often made of stainless steel or specialized alloys.
- Plastics (PVC/CPVC/UPVC): Used for valve bodies and discs in applications requiring high corrosion resistance, particularly with certain acids and chemicals, often at lower pressures and temperatures. Options like a UPVC electric butterfly valve provide automated control for corrosive media lines.
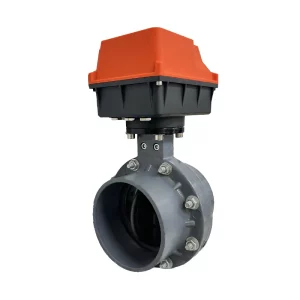
UPVC electric butterfly valve
Selecting the right materials ensures chemical compatibility, prevents premature failure due to corrosion or degradation, and maximizes the service life and durability and performance of the butterfly valve. As manufacturers, we offer guidance on material selection based on the specific variety of applications and operating conditions.
Where are Butterfly Valves Most Effectively Used? A Look at Applications
The versatility, cost-effectiveness, and ease of operation make butterfly valves suitable for a vast variety of applications across numerous industries. Their ability to handle large fluid flows with a relatively compact design is a major advantage. Butterfly valves are used extensively in:
- Water and Wastewater Treatment: This is a primary area. Butterfly valves are ideal for controlling the flow of potable water, raw water, wastewater, sludge, and seawater. Their relatively low cost and availability in large diameters make them perfect for municipal water distribution, treatment plants, and pumping stations. Robust options like the Ductile iron electric butterfly valve are frequently specified according to American Water Works Association (AWWA) standards for these demanding environments.
- HVAC Systems: In commercial and industrial heating, ventilation, and air conditioning (HVAC systems), butterfly valves are commonly used for isolating equipment (chillers, boilers, cooling towers) and controlling water flow in heating and cooling loops. Their quarter-turn operation is convenient for maintenance personnel. They often work alongside other components like balancing valves to ensure proper system performance; for specific balancing needs, a Ductile iron balancing valve(SP45F-10/16) might be used.
- Chemical Processing: Depending on material selection (316 stainless steel, alloys, PTFE/ Viton seats), butterfly valves can be used for handling various chemicals, acids, and bases. High performance butterfly valves (double offset, triple offset) are often required for corrosive or high-temperature chemical services.
- Power Generation: Butterfly valves find use in cooling water systems, circulating water lines, and flue gas desulfurization (FGD) systems in power plants. Large diameter valves are common here.
- Oil and Gas: While ball valves and gate valves are often preferred for critical hydrocarbon applications, butterfly valves (particularly high performance types) are used in utility lines, cooling systems, and some lower-pressure process streams within refineries and processing plants.
- Pulp and Paper: Butterfly valves handle water, white water, liquors, and stock slurries in paper mills. Abrasion and corrosion resistance are key considerations here.
- Food and Beverage: Stainless steel butterfly valves with sanitary finishes and appropriate seat materials (like EPDM or silicone) are used in hygienic applications for controlling the flow of liquid food products, beverages, and cleaning solutions.
- Shipbuilding and Marine: Used extensively for seawater cooling systems, ballast systems, and other onboard fluid handling due to their space-saving design and resistance to corrosion (when appropriate materials are chosen).
- Fire Protection Systems: Butterfly valves are frequently used in pipelines for fire control, often listed/approved by relevant safety organizations (like UL/FM). They serve as control and shut-off valves in sprinkler systems and fire hydrants. Their quick operation is advantageous in emergencies.
The wide range of sizes available, from small diameters up to very large ones (several meters), further enhances their applicability. Valves play an important role in controlling flow in nearly every industrial and municipal process, and the butterfly valve is often a go-to choice for many general-purpose and specialized tasks.
Why Choose a Butterfly Valve Over Other Valve Types like Gate or Ball Valves?
While various valve types exist for controlling flow, butterfly valves offer distinct advantages in many situations, making them a preferred choice over traditional options like gate valves or even ball valves for certain applications.
- Cost-Effectiveness: Butterfly valves generally have a simpler design with fewer components compared to gate or globe valves, especially in larger sizes. This translates to lower manufacturing costs and a more economical purchase price.
- Space and Weight Savings: Their compact, wafer or lug style bodies are significantly lighter and require less installation space than bulky gate or globe valves of the same pipe size. This is a major benefit in crowded piping systems or where structural support is a concern.
- Ease and Speed of Operation: Being a quarter-turn valve, a butterfly valve can be fully opened or closed with a simple 90-degree turn of the handle or actuator. This is much faster than the multi-turn operation required for gate or globe valves, which is advantageous for quick shut-off.
- Lower Torque Requirements (Generally): Especially in lower pressure applications, butterfly valves require less torque to operate than gate valves, potentially allowing for smaller, less expensive actuators. However, hydrodynamic torque can become significant at certain disc positions and flow rates.
- Good Throttling Capability (with limitations): While not as precise as globe valves, butterfly valves can be used for throttling flow, particularly high performance designs. Ball valves can also throttle but may experience seat wear in partially open positions.
- Suitability for Large Diameters: Butterfly valves are readily available and relatively economical in very large sizes (DN > 600), where gate or ball valves become prohibitively large, heavy, and expensive.
However, there are also considerations where other valves might be better:
- Pressure Drop: Butterfly valves inherently have the disc remaining in the flow path even when fully open, creating more pressure drop and flow obstruction than a full-bore gate valve or ball valve.
- Sealing: While modern butterfly valves offer excellent sealing (especially resilient seated and triple offset), achieving a perfect bubble-tight seal can sometimes be more challenging than with certain ball valve designs, particularly in critical gas applications.
- Slurries: The disc can be susceptible to wear in highly abrasive slurries, where a knife gate valve or a specialized ball valve might be more suitable.
Ultimately, the choice depends on the specific application requirements, including pressure, temperature, fluid type, required flow characteristics (on/off vs. throttling), size, and budget. As manufacturers of diverse valve solutions, we help customers weigh these factors to find the optimal product.
Understanding Pressure Ratings and Performance in Butterfly Valves
The pressure rating and overall performance characteristics are critical factors when selecting a butterfly valve. These define the valve’s ability to withstand the operational stresses of the system safely and effectively.
- Pressure Rating (e.g., ANSI Class, PN): This indicates the maximum pressure the valve body and components can safely handle at a given temperature. Common ratings include ANSI Class 150, 300, etc., or PN10, PN16, PN25 in metric systems. The rating typically decreases as the operating temperature increases. Exceeding the pressure rating can lead to catastrophic failure. Ratings are often specified in psi (pounds per square inch) or bar. Butterfly valves are available across a wide range of pressure classes, from low-pressure HVAC applications to high-pressure industrial processes, especially with high performance butterfly designs (double offset, triple offset).
- Differential Pressure: This is the pressure difference across the valve disc when closed. The actuator must generate sufficient torque to overcome this differential pressure, plus friction, to open the valve. Larger butterfly valves or those operating under high differential pressure require significant torque.
- Temperature Limits: Materials used in the valve (especially the seat – EPDM, Viton, PTFE, metal) dictate the minimum and maximum operating temperatures. Exceeding these limits can cause seat failure, leakage, or damage to other components.
- Flow Coefficient (Cv or Kv): This value quantifies the valve’s capacity for fluid flow. A higher Cv indicates less flow restriction when the valve is fully open. While butterfly valves offer good flow capacity, the disc always presents some obstruction.
- Sealing Performance: This defines how well the valve prevents leakage in the closed position. Resilient seated valves typically offer Class VI (bubble-tight) shutoff at lower pressures. High performance metal-seated valves (triple offset) can also achieve bubble-tight shutoff even at pressure and high temperatures. Leakage class standards (e.g., API 598, MSS-SP-61) specify allowable leakage rates.
- Torque: The rotational force required to operate the valve. This depends on valve size, design (concentric vs. eccentric), pressure differential, seat material friction, and fluid properties. Accurate torque calculation is essential for sizing the actuator correctly.
Understanding these parameters ensures the selected butterfly valve can handle pressures, temperatures, and flow conditions reliably throughout its intended service life, contributing to overall system safety and efficiency.
Key Considerations for Installation and Maintenance
Proper installation and regular maintenance are vital for ensuring the optimal performance and longevity of butterfly valves. Neglecting these aspects can lead to premature failure, leakage, and operational issues.
Installation:
- Pipe Alignment: Ensure the mating pipe flanges are properly aligned and parallel. Misalignment stresses the valve body and can cause uneven loading on the seat, leading to leakage.
- Flange Spreading: Use appropriate tools to spread the flanges just enough to insert the wafer or lug style valve without damaging the seat face. Avoid using the valve disc itself to pry the flanges apart.
- Bolting: Tighten flange bolts gradually and evenly in a star or crisscross pattern to ensure uniform gasket compression and prevent warping the valve body. Follow recommended torque specifications for the bolts. For lug butterfly valves, ensure all bolts are engaged correctly.
- Disc Position: During installation, the disc should ideally be in a slightly open position (approx. 10 degrees) to prevent it from being pinched or damaged by the pipe flanges as the bolts are tightened. Check manufacturer recommendations.
- Flow Direction: While many butterfly valves are bi-directional, some high performance designs may have a preferred flow direction for optimal sealing or performance. Check the valve markings or manual.
- Protection: Keep protective covers on flange faces and valve internals until the moment of installation to prevent dirt or damage.
Maintenance:
- Regular Inspection: Periodically check for external leaks (stem packing, flange joints), signs of corrosion, or physical damage.
- Actuation Check: Operate the valve through its full cycle occasionally (if feasible within the process) to prevent seizing and ensure the actuator (manual or powered) is functioning correctly. Lubricate gear operators or manual actuators as per manufacturer guidelines.
- Seat Integrity: While internal inspection often requires removal, monitor for any signs of internal leakage when the valve is closed, which might indicate seat wear or damage.
- Stem Packing: For valves with adjustable packing glands, tighten slightly if stem leakage occurs. Overtightening increases operating torque and can damage the stem. Repacking may be necessary over time.
- Environment: Ensure the operating environment (temperature, external corrosive elements) remains within the valve’s specifications.
Preventive maintenance schedules should be based on the severity of service, cycle frequency, and manufacturer recommendations. Butterfly valves require relatively less maintenance than some other valve types, but these basic checks help maximize service life and reliability.
The Rise of Smart Technology in Butterfly Valves
The integration of smart technology is transforming how butterfly valves are monitored, controlled, and maintained, particularly in building automation, industrial processes, and water treatment facilities. As manufacturers at the forefront of this evolution, we see increasing demand for valves equipped with advanced communication and diagnostic capabilities.
Smart butterfly valves typically incorporate electric actuators with embedded sensors and communication modules. This allows them to:
- Remote Control & Monitoring: Operators can open, close, or throttle valves remotely via control systems (SCADA, BMS, PLC) using protocols like Modbus RS485, or wireless technologies such as LoRaWAN, NB-IoT, 4G, or WiFi. Integration is often achieved using components like an RS485 rotary actuator coupled with the valve.
- Real-Time Feedback: Provide precise feedback on the valve disc position (not just fully open/closed, but percentage), operating torque, cycle counts, and internal temperature.
- Predictive Maintenance: By monitoring parameters like operating torque and cycle time, smart actuators can predict potential issues like increased friction (due to wear or scaling) or actuator degradation before failure occurs, enabling proactive maintenance scheduling.
- Diagnostics: Log operational data and fault codes, aiding in troubleshooting and reducing downtime. Some can even detect obstructions or abnormal pressure conditions.
- Energy Efficiency: Enable optimized control strategies in HVAC systems or industrial processes, reducing energy consumption by ensuring valves operate precisely as needed. A smart RS485 regulating valve, which might utilize a butterfly body, exemplifies this precise control capability.
- Integration: Seamlessly integrate into IIoT (Industrial Internet of Things) platforms for centralized data analysis and system-wide optimization.
These smart capabilities are invaluable for applications requiring high reliability, remote accessibility, or integration into complex automated systems. While the initial cost might be higher than a standard butterfly valve with a basic actuator, the benefits in terms of reduced maintenance, improved operational efficiency, enhanced safety, and extended service life often provide a rapid return on investment, particularly in critical variety of applications like water and wastewater treatment or large industrial facilities.
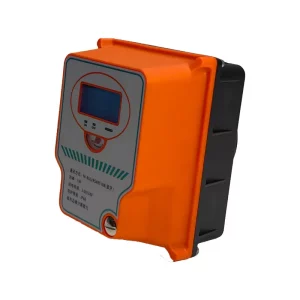
RS485 rotary actuator
FAQs about Butterfly Valves
What is the main disadvantage of a butterfly valve?
The primary disadvantage is that the disc always remains in the flow path, even when fully open. This creates a pressure drop across the valve, which is generally higher than that of a full-bore gate valve or ball valve. This pressure drop can be significant in systems where flow efficiency is paramount. Also, standard concentric designs may have limitations in very high-pressure or abrasive slurry applications compared to specialized valves.
Are butterfly valves good for throttling?
Butterfly valves can be used for throttling flow, but their performance varies. High performance butterfly valves (double and triple offset) generally offer better throttling characteristics and control range than basic concentric designs. However, for precise flow control over a wide range, globe valves are often superior. Throttling in a butterfly valve can sometimes increase turbulence and potential wear on the disc and seat, especially near the closed position.
How long do butterfly valves typically last?
The service life of a butterfly valve depends heavily on the application (fluid type, pressure, temperature), materials of construction, frequency of operation (cycling), and proper installation/maintenance. A well-chosen, correctly installed butterfly valve in a clean water application might last 10-20 years or longer, while one in severe chemical service or frequent high-cycle operation might require maintenance or replacement much sooner. High performance designs generally offer longer life in demanding conditions.
Can butterfly valves be used for gas?
Yes, butterfly valves are commonly used in pipelines for various gas applications, including air, natural gas, and process gases. However, sealing performance is critical for gas service. Resilient seated butterfly valves can provide tight shutoff for lower pressure gas, while triple offset butterfly valves are often preferred for high-pressure gas or applications requiring zero leakage (bubble-tight shutoff) due to their metal-to-metal sealing. Material compatibility with the specific gas is also essential.
What is the difference between a lug and wafer butterfly valve?
The main difference lies in how they mount between pipe flanges. A wafer butterfly valve is sandwiched between flanges using long through-bolts that clamp the entire assembly together. A lug butterfly valve has threaded inserts (lugs) around its body, allowing it to be bolted directly to each flange independently. This means a lug valve can be used for end-of-line service (one side of the piping can be removed while the valve stays attached), whereas a wafer valve cannot.
Are butterfly valves bidirectional?
Most standard concentric and many double offset butterfly valves are designed to be bi-directional, meaning they can seal against flow and pressure from either direction. However, some high performance designs, particularly triple offset valves, may have a preferred flow direction for optimal sealing performance or to achieve their specified pressure rating. Always check the manufacturer’s specifications or valve markings.
Key Takeaways
- Butterfly valves are quarter-turn valves offering a compact, lightweight, and cost-effective solution for flow control (shut-off and regulation) of liquids and gases.
- Key components include the valve body, disc, stem, and seat; material selection (EPDM, Viton, stainless steel, etc.) is critical for compatibility and service life.
- Common types include wafer (sandwiched) and lug (bolted, end-of-line capable) body styles.
- Designs range from concentric (simple, low pressure) to eccentric (double offset, triple offset) for high performance, higher pressures, and temperatures.
- Actuation can be manual (lever, gear) or powered (electric, pneumatic, hydraulic), with smart actuators offering remote control and diagnostics.
- They are widely used in pipelines across water and wastewater treatment, HVAC, chemical processing, power generation, and fire protection systems.
- Installation requires proper alignment and bolting; maintenance involves regular inspection and operation checks.
- Smart butterfly valve technology enhances control, monitoring, and predictive maintenance capabilities, crucial for modern automated systems.
As experienced smart valve manufacturers, we understand the nuances of butterfly valve selection and application. Contact us to discuss your specific requirements for high-quality, reliable valve solutions tailored to your needs.
string(149) "https://www.navarchjncn.com/news/choosing-the-right-balancing-valve-a-guide-to-types-automatic-balancing-and-premium-residential-valves-and-fittings/"